How can you save up to 50% energy with SCR compressors?
Find out how much you can save with SCR-PM2 compressors
Energy first!
It always pays to think about the future, and this is doubly true if you're thinking of buying a new screw compressor. With a compressor that you will run for 10 to 20 years, you will have a number of costs associated with it, such as the purchase of the machine, its installation, regular maintenance or dealing with breakdowns. However, the main cost is the electricity needed for machine run.
Based on our experience, electricity costs account for more than 80% of all costs over a 10-year time horizon. This is roughly 14 times more than the purchase price of a compressor. It is therefore definitely worth finding out about how economical the machine you are considering is before you buy it.
Especially at a time of extreme growth in electricity bills…
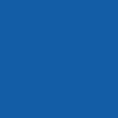
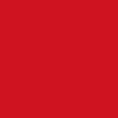
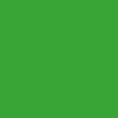
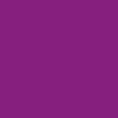
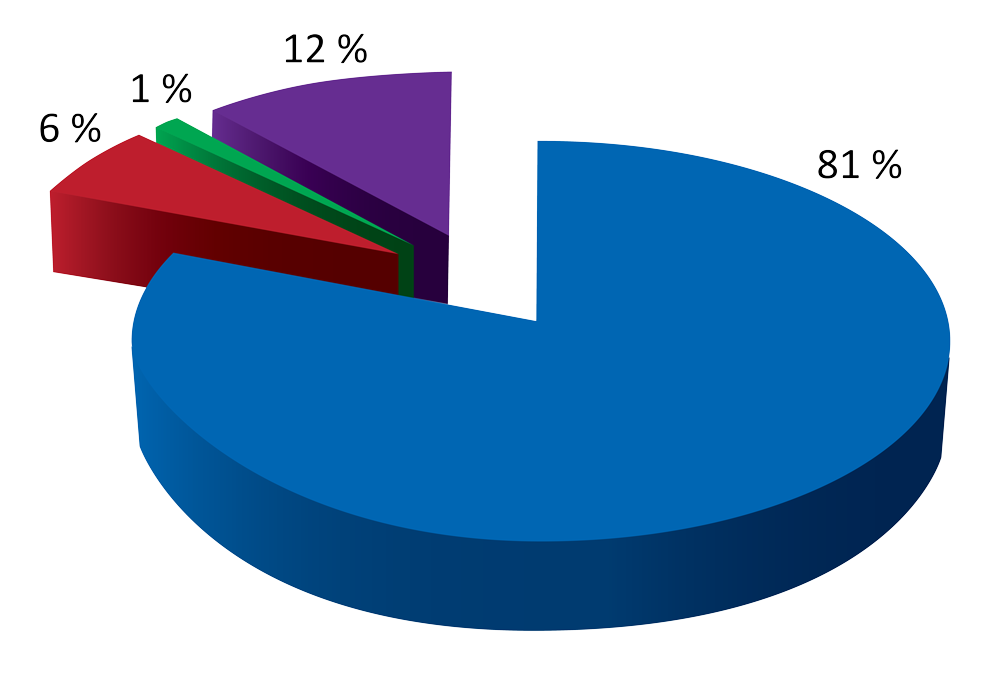
SCR compressors saving solutions
All SCR compressor series have been designed with the highest possible energy efficiency in mind and feature many innovative and advanced features to help reduce the cost of electricity and compressed air production in the industrial and energy sectors. Solutions that help reduce the cost of compressor operation include:
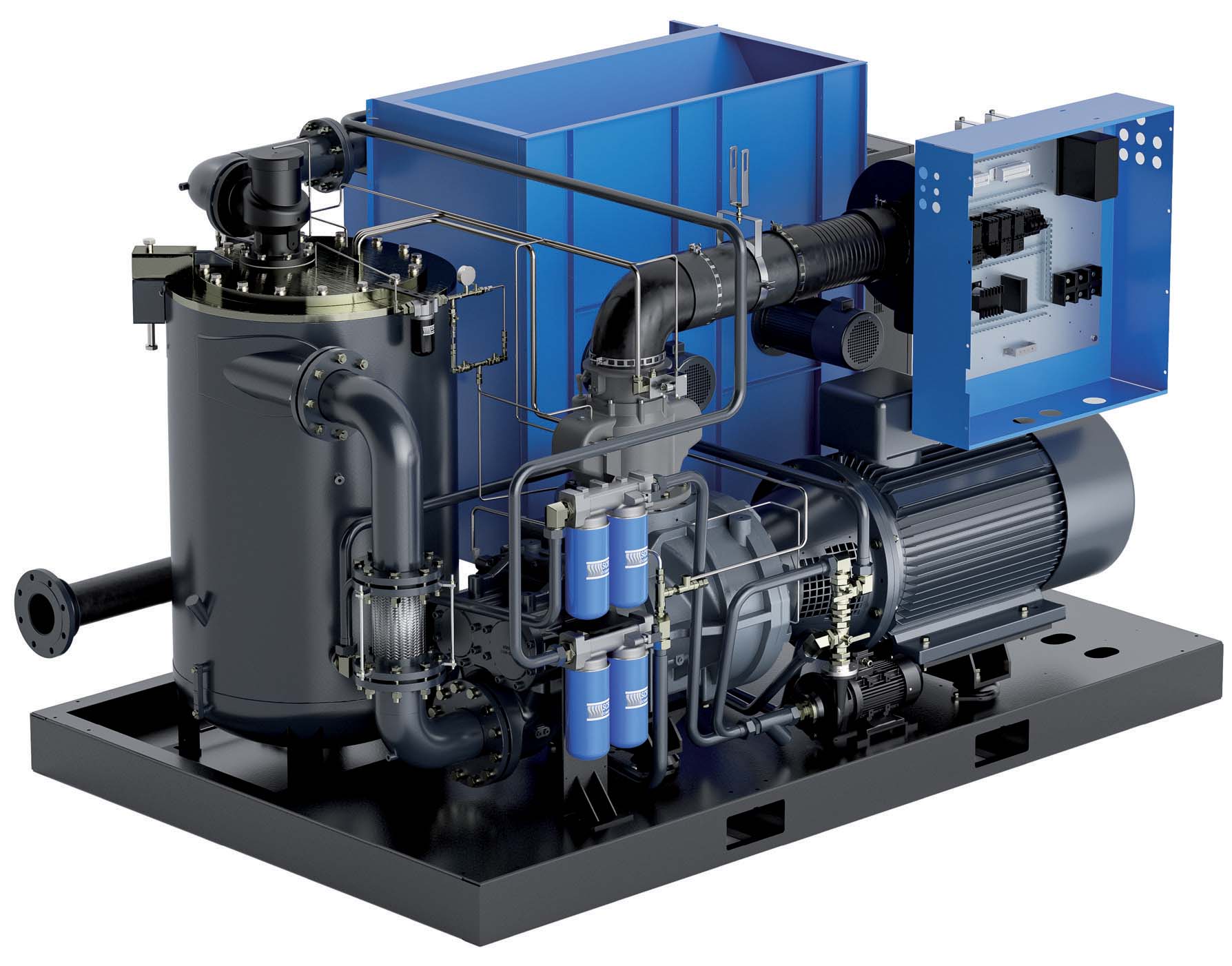
- variable speed control
- two-stage compression
- lossless direct drive
- permanent magnet motor IE4
- output pressure setting
- economical weekly plan
- fan with speed control
- low pressure designs
- oil-free compressors
Variable speed control
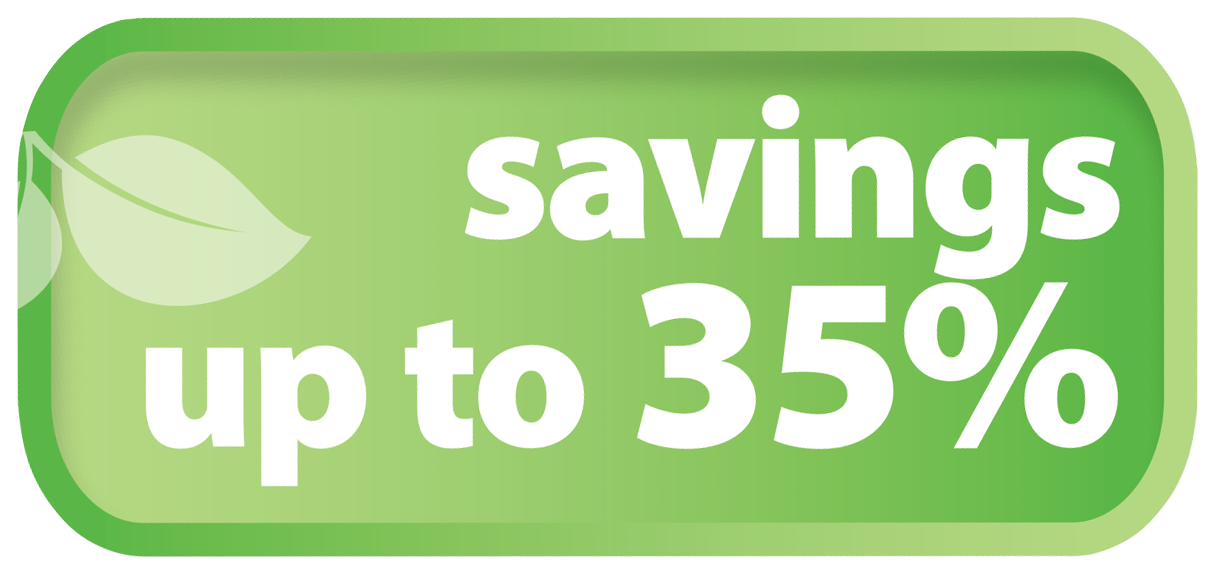
There are two basic ways of controlling compressor operation on the market:
- fixed speed (FS) compressors
- compressors with continuous speed control by means of frequency converter (variable speed drive - VSD)
Fixed speed compressors have two pressure settings - switching on and off. If the pressure drops below the cut-off value, the compressor switches on the main motor and starts producing compressed air.
As soon as it reaches the cut-off pressure, the compressor switches off in such a way that it first goes into idling (also relief), when the motor and the airend rotate, but the suction valve is switched off and the compressor does not produce air. Only after a certain time, in the order of a few tens of seconds to a few minutes, the machine is completely switched off.
Two-stage compressors
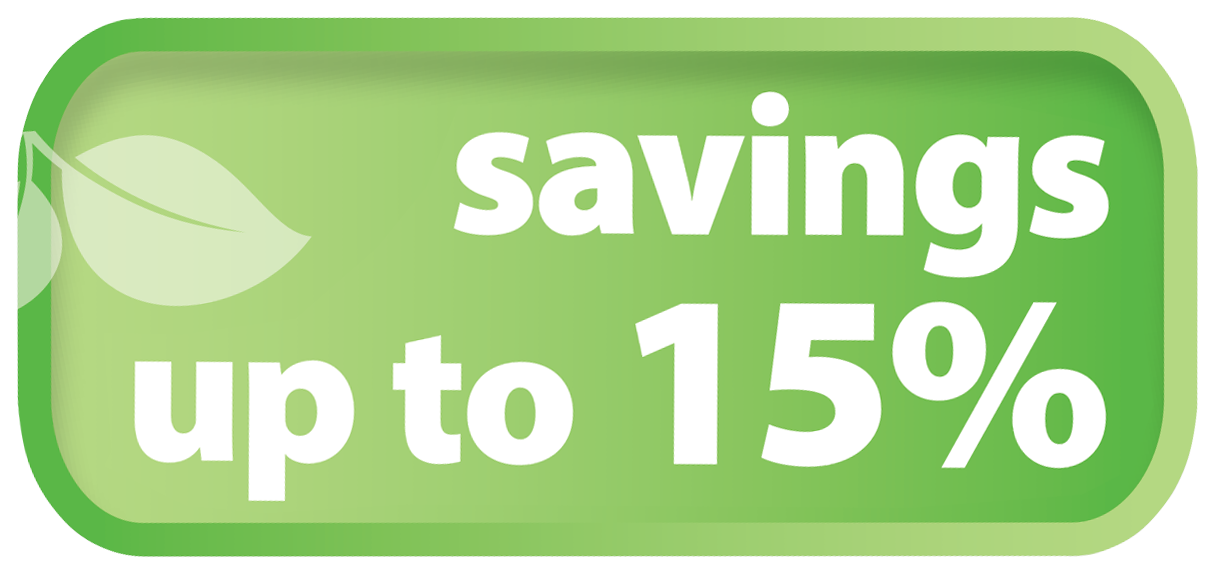
Standard screw compressors use only one airend for air compression. Compression to the desired pressure thus occurs in only one step, the so-called stage. The advantage of single-stage compression is low cost, but from an energy point of view this method is not economical.
During air compression, a significant part of the supplied energy is converted into heat and the consequence of this phenomenon is a reduction in efficiency and the production of significantly less air compared to the ideal physical process in the so-called isothermal state, when all the supplied energy is used exclusively for gas compression and no heat is generated. For higher compression efficiency, two-stage compressors have been developed that use 2 airends connected to each other by a gear train.
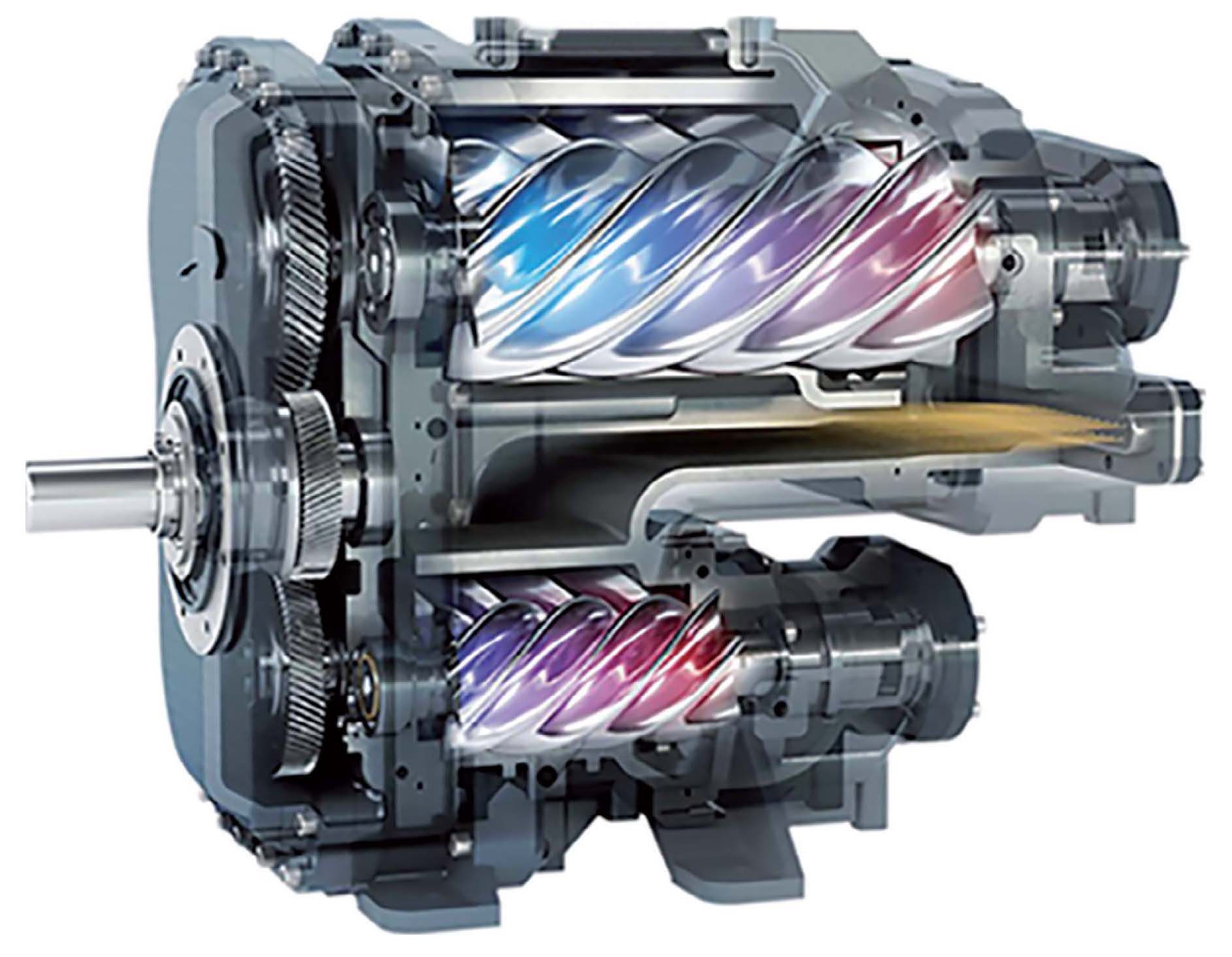
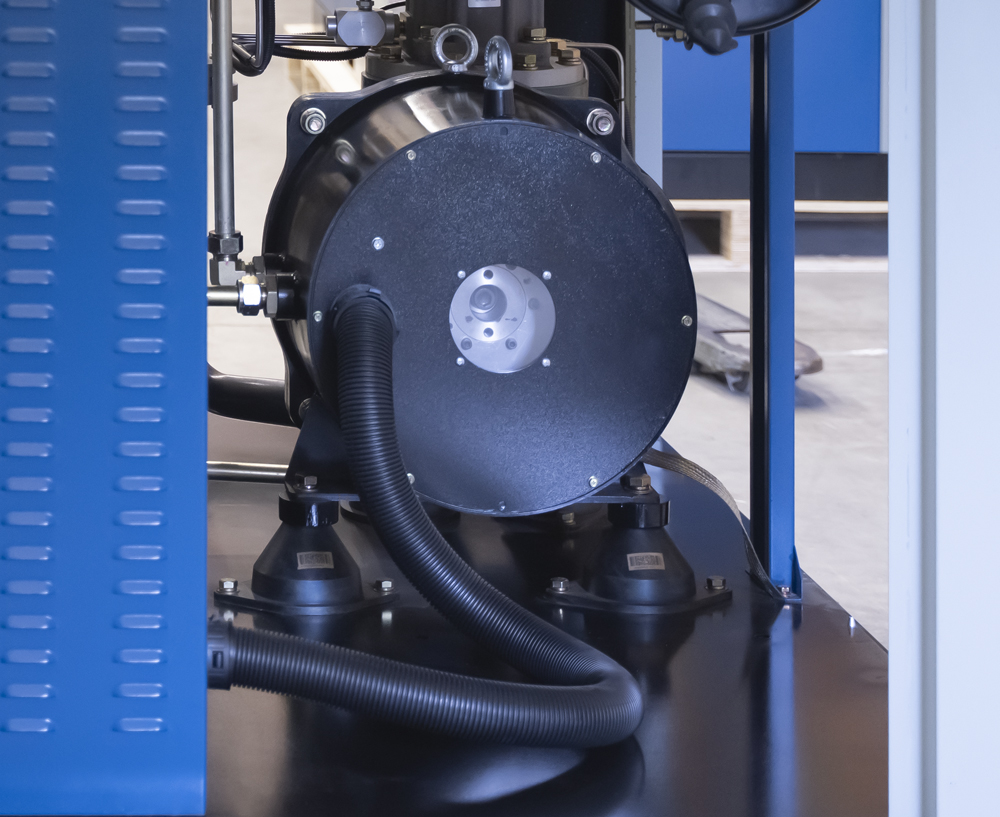
Electric motor IE4 with permanent magnets
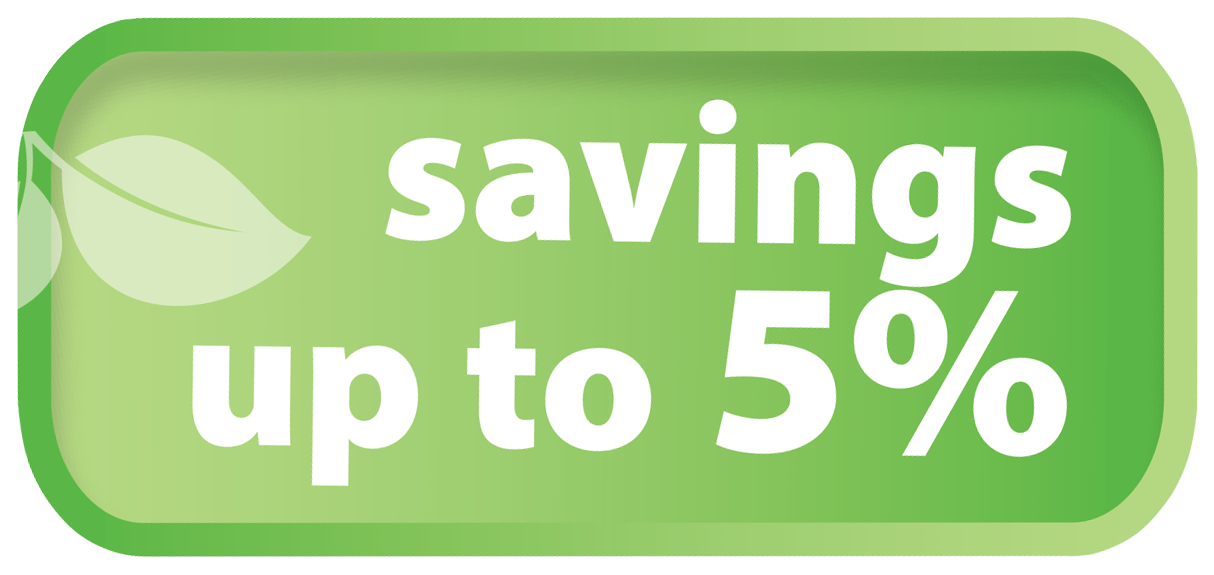
Electric motors used on compressors must, according to IEC EN 60034 from January 1, 2017 have an efficiency of at least IE3 for power inputs from 0.75 kW, and IE2 is sufficient for speed control.
However, modern compressors use higher efficiency electric motors and the most well-known solution is permanent magnet (PM) motors, whose efficiency exceeds IE4 efficiency requirements. The differences in efficiency and energy savings achieved between IE3 and IE2 standards and PM motors on SCR machines can be found in the table below and typically 2 - 5% energy savings can be achieved compared to IE2 versions.
No loss direct drive 1:1
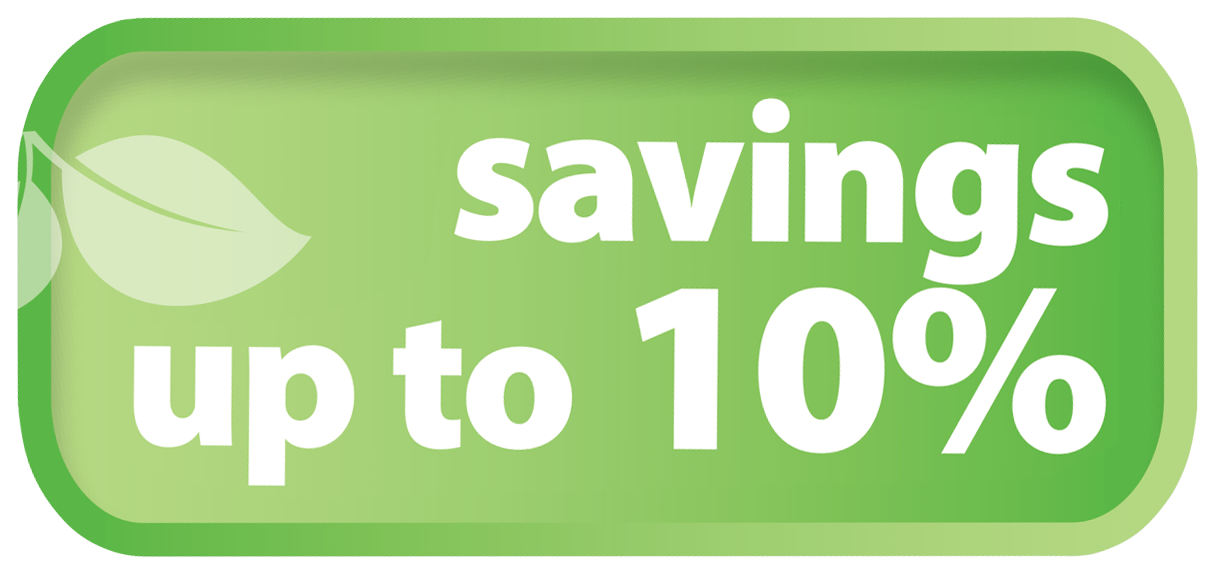
The transmission between the airend and the electric motor is realized in four ways in screw compressors:
- using V-belts
- elastic coupling
- gearbox
- direct coupling, the characteristics of which depend greatly on whether it is used in conjunction with a conventional electric motor or in conjunction with a permanent magnet bearingless motor.
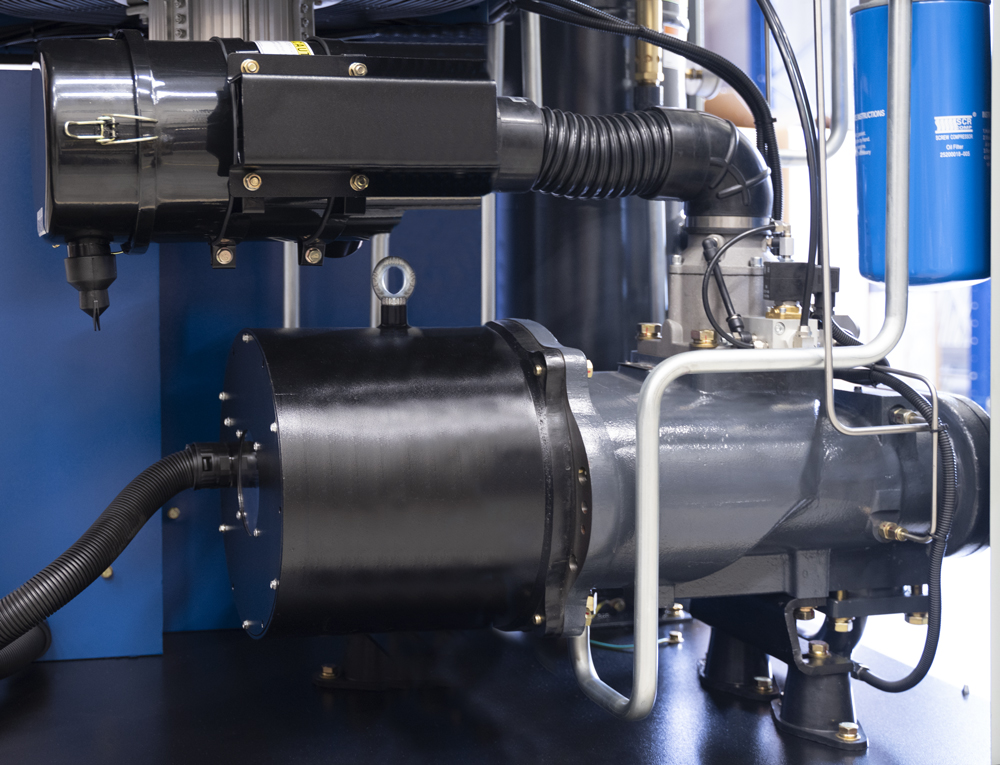
Flexible pressure adjustment
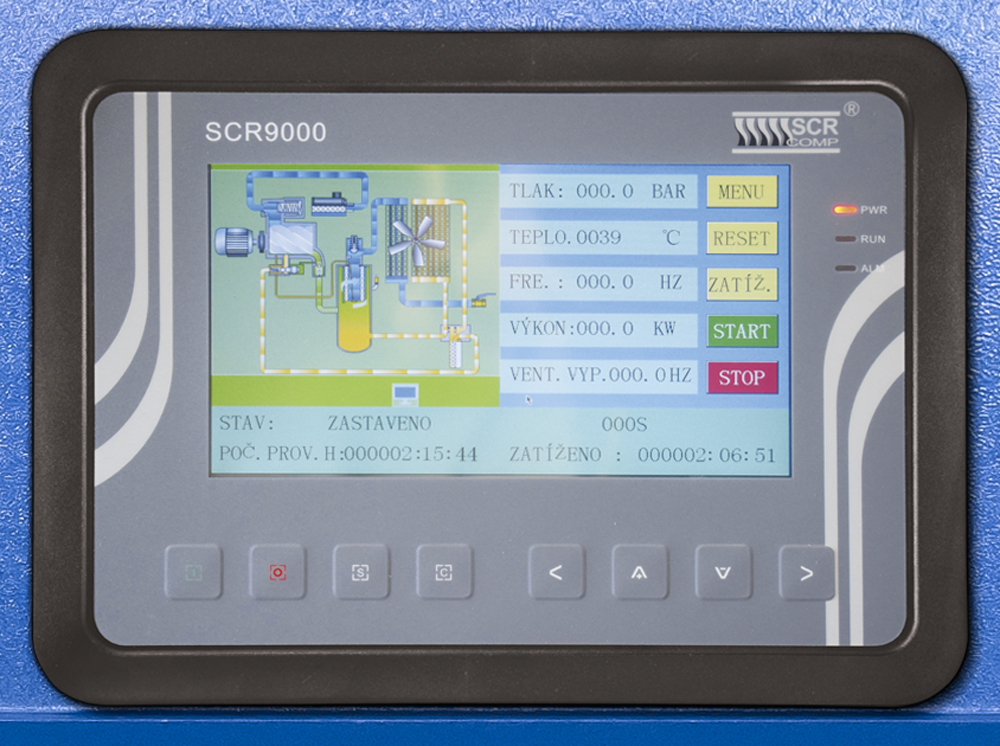
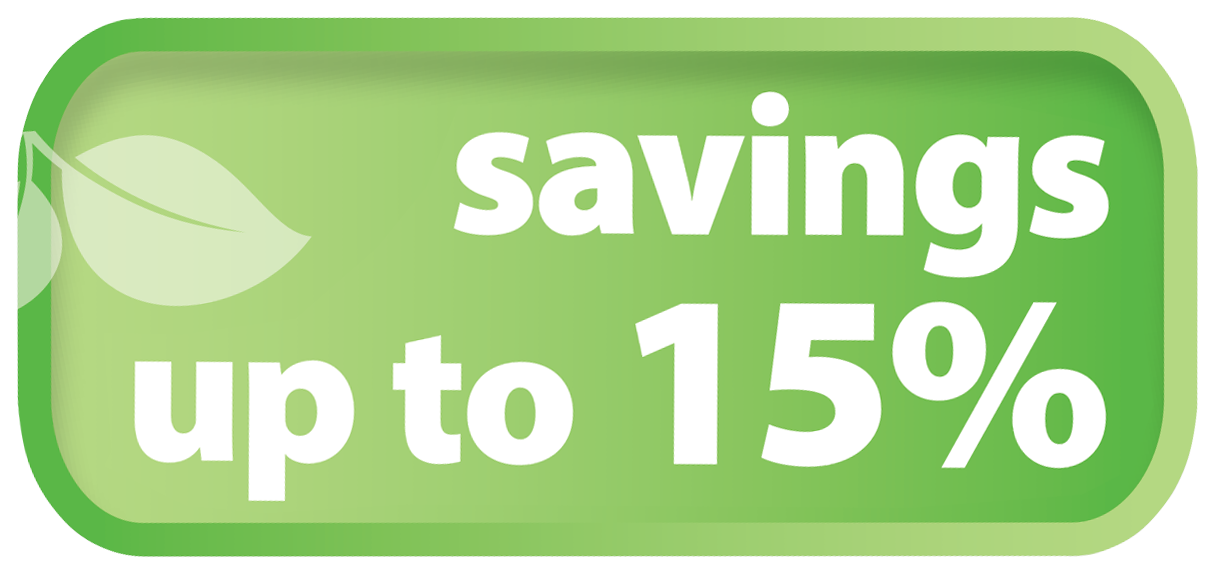
Compressing the air consumes energy. The higher the pressure, the more energy the compressor needs to achieve it. Always keep in mind that:
An extra 1 bar of air compression means approximately 7% of the energy expended!
A well-chosen compressor should therefore have an output pressure slightly above the required level, so that it does not consume unnecessary energy for excessive compression, which will then be released. Unfortunately, we often witness situations where the user operates a compressor with a supplied pressure of, for example,
10 bar and then the pressure is reduced to, for example, 6 bar on all input regulators to the machines. Judge the economics of such a solution for yourself…
Smart compressor shutdown
A major problem in manufacturing plants is the presence of compressed air leaks, which are usually around 20%, but significantly higher values can be encountered. Leaks in the piping system are always present, even when production is not taking place, e.g. at the weekend, at night or during breaks between shifts. It is therefore extremely convenient to turn off the compressors temporarily during this time so that they do not produce air only to cover leaks in the air pipe network.
On modern controllers used on SCR compressors, it is possible to set a weekly schedule for compressor operation and set several periods of time each day from Monday to Sunday when the compressor is on and when it is off.
Model example
Manufacturing plant with air leakage of 20% of air consumption and 2-shift operation with free weekend
by switching off the compressor during off-shift hours, you save 0.52 × 0.2 = 10.4%
Day | Time from | Time to | Status |
Mon - Fri | 0:00 | 5:59 | off |
6:00 | 21:59 | on | |
22:00 | 23:59 | off | |
Sat - Sun | 0:00 | 23:59 | on |
Low pressure applications 1,5-5 bar
In industry there are many applications that need lower pressure than the common 7 - 10 bar supplied by screw compressors. Such applications are most often found in the glass, plastics, textile or cement industries and require compressed air pressures of typically 1.5 to 5 bar.
In these so-called low pressure applications, it is not sufficient to produce air using blowers, whose upper limit of pressure performance ends at an overpressure of about 1.5 bar, and therefore conventional screw compressors are used, which have an output pressure of about 7-10 bar. Although speed controlled compressors allow reducing the delivered pressure to a level of 4 - 5 bar, they face 2 major problems:
pressure range 4 - 5 bar - conventional compressors are not optimised for 4 - 5 bar and energy efficiency is very poor in this range
pressure range 1.5 - 4 bar - compressors must produce a pressure of at least 4 bar anyway, which is then reduced to the required pressure in the range of 1.5 - 4 bar
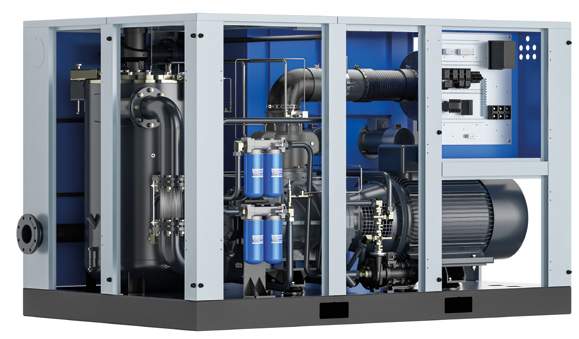
Oil-free compressors
Some critical industrial applications require the supply of oil-free compressed air. These are mainly in the beverage industry, the food industry, the hospital and pharmaceutical sectors, and the supply of industrial breathable air for blasting or paint shops. Oil-free compressed air is defined by ISO 8573-1 as Class 0 and can be produced either by a conventional compressor with an appropriate air treatment system or directly by an oil-free compressor.
The use of oil-free compressors is becoming more and more suitable even outside these critical applications, mainly because of the zero risk of air quality reduction due to oil leakage, but also because of the significantly lower investment and maintenance costs of the technology.
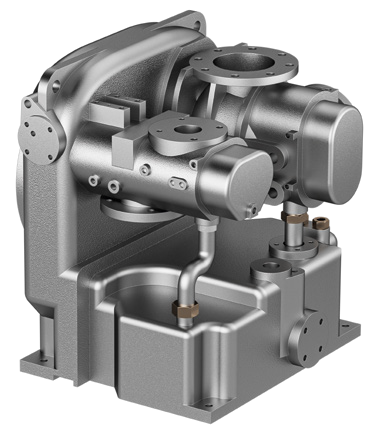
The main savings of oil-free compressors:
- no need to install filters and activated carbon columns
- no need to install water oil separator
- no oil changes
- no oil and separation filter changes in the compressor
- no need to clean the oil cooler
- no maintenance of thermostatic valve and check valve
- solid particle filter elements have longer maintenance
- no need to replace separator cartridges
- no need for condensate quality tests
- no waste water legislation
- eliminates oil receiver pressure inspections of the oil reservoir in the compressor
Speed controlled fan
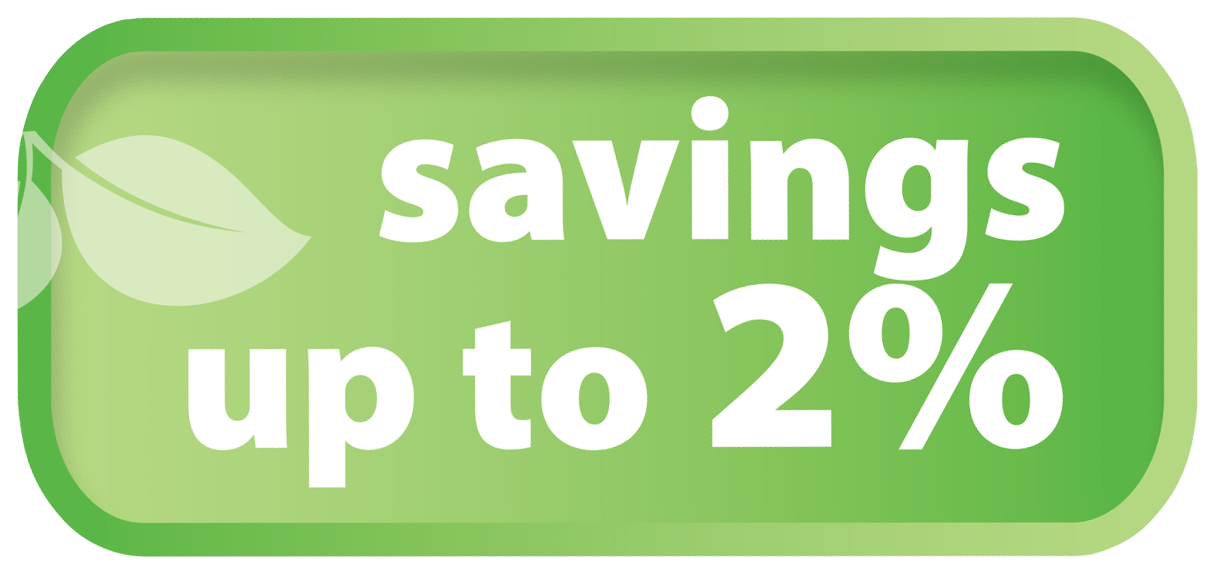
Each compressor is equipped with a fan that provides exhaust for the hot air present inside the compressor and provides cooling for the oil and air cooler.
The energy consumption of the fan is typically 2 to 5% of the total power input of the compressor.
Thanks to the regulation, the fan motor only draws the actual amount of electricity needed and, compared to the traditional solution where the fan runs completely unregulated, the electricity consumption is extremely reduced by tens of percent, which means a few percent of the total energy consumption of the compressor.
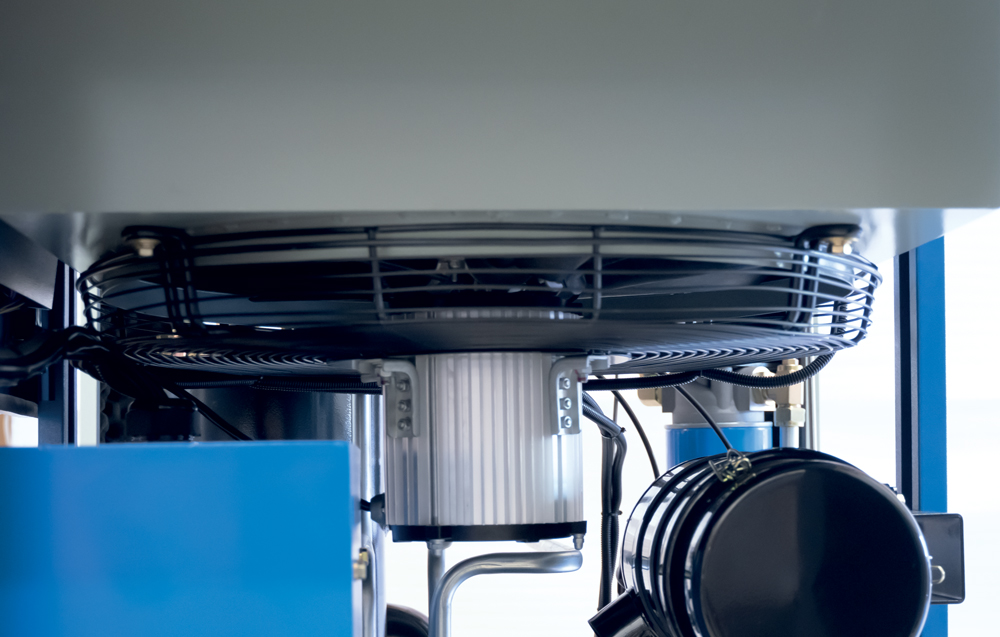
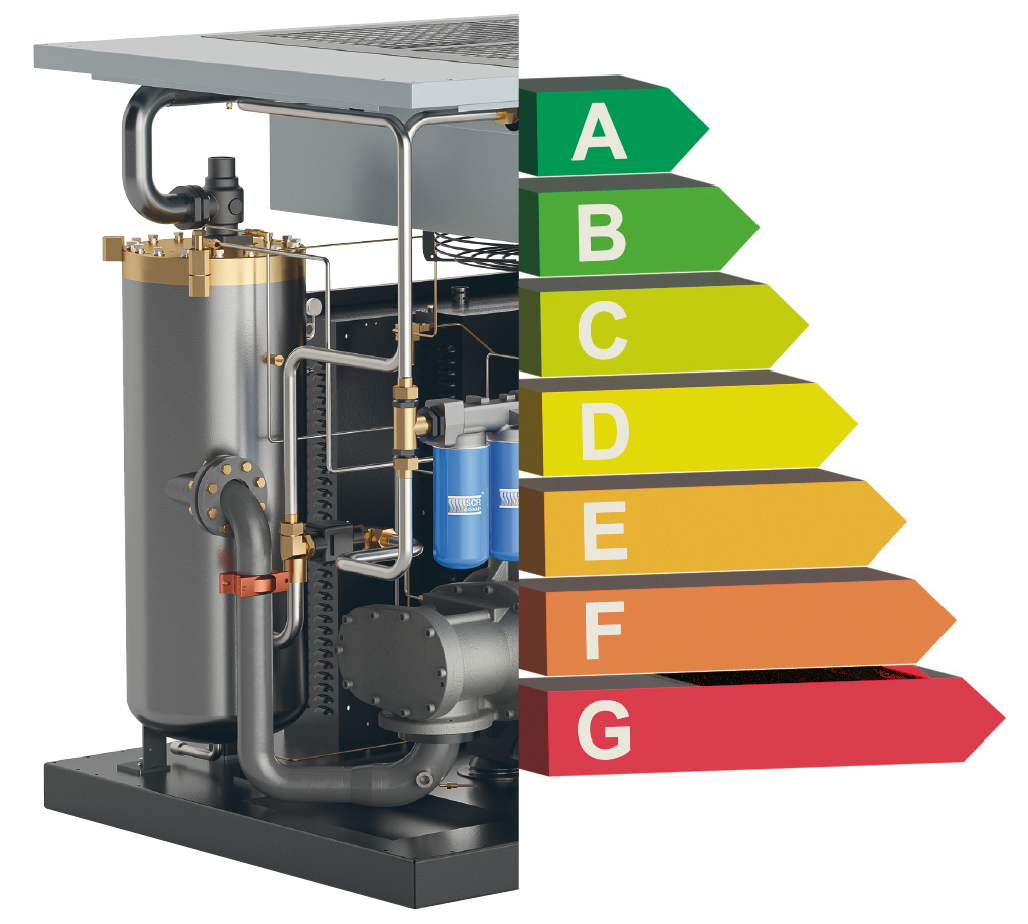
SCR AUDIT - find out how much you can save!
If you need help to achieve energy savings and are not sure what the optimal solution is, contact our company.
We have a lot of experiences with compressor room design and energy cost optimization in existing compressor rooms, based on which we have prepared a concept for the assessment of the current situation in the form of an SCR AUDIT.
If you decide to use SCR AUDIT, we will visit your facility and conduct an audit as part of the process:
- comprehensive assessment of the current state of compressors
- assessment of the air treatment system
- measurement of compressed air consumption
- detection and quantification of air leaks
Energy savings
You will find more detailed information on energy savings in the enclosed leaflet.
EN version, PDF - 2,80 MB.